
Common types of corrosion that are seen within industrial, marine/offshore and oil and gas include 5 main categories. These are what we will cover in this blog post, including suggestions on how to prevent it.

Metals that are attacked by corrosive substances are open to damage that can effect the durability and safety of the alloy. This is a huge concern for sectors of industry with environmental considerations. For example, within the marine and offshore industries, engineers will require metals that can withstand exposure to seawater.
Common Types Of Corrosion
1. Galvanic Corrosion
Galvanic corrosion will occur when two separate metals/alloys are in contact with each other. This type of corrosion will occur when
a) When metals are electrochemically dissimilar
b) Metals are in electrical contact
c) Metals are exposed to electrolyte
2. Uniform Corrosion
Irons and steels will corrode in ‘uniform’ when exposed to certain environments such as soils and natural waters. Rust will appear in the presence of uniform corrosion.
3. Pitting Corrosion
Spots and pits will appear on the metal with this type of corrosion. It is a type of localised corrosion, which means that the attack is accelerated due to exposure of an area on the metal that an otherwise protective coating or layer has broken down.
4. Stress Corrosion Cracking
Unexpected sudden failure can occur with this type of corrosion. Attack of an alloys tensile strengths at high temperatures is a common situation for stress-corrosion cracking.
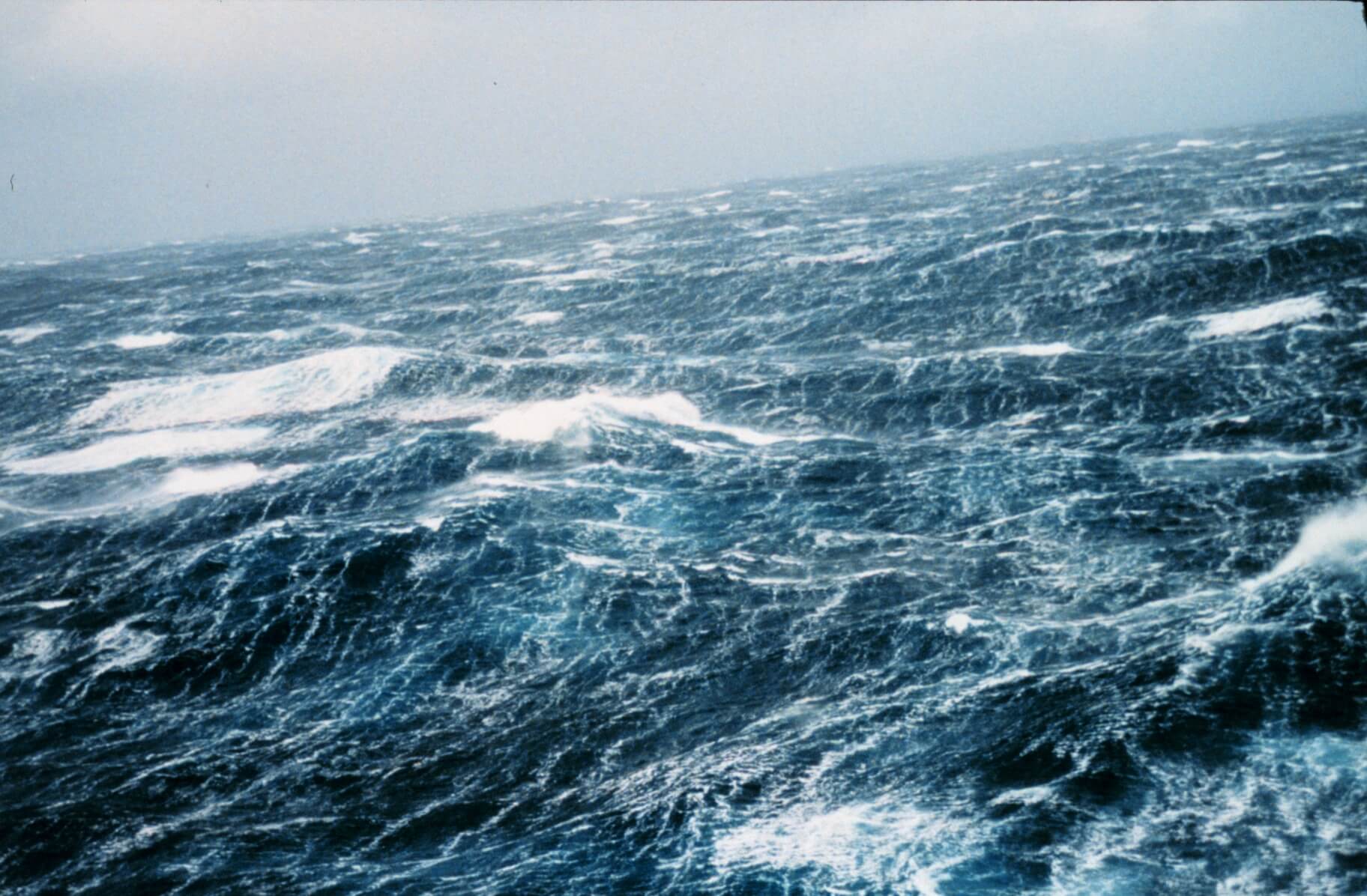
5. Aqueous Corrosion
“Aqueous corrosion is an electrochemical reaction of materials due to a wet environment, resulting in the deterioration of the material and its vital properties.” – What Is Aqueous Corrosion by Corrosionpedia.com
Corrosion Prevention
There are various ways to prevent the effects of corrosion. Each type of corrosion will differ in the prevention method.
However, generally, the selection of the correct corrosion resistant metal to begin with can prevent needing further treatments and prevention methods.
some prevention methods that need consistent updating and maintenance can be a hassle – both economically and practically. An investment of a high-performance alloy will save much of this hassle.
It is very important to note that each corrosion resistant metal has its own properties and composition that will cope with some types of corrosion better than another.
This is why the selection of the right material is vital for cost, availability and most importantly – safety.
Material Selection And Advice
Corrosion Problem | Solution |
---|---|
Galvanic Corrosion | Avoid mixing fittings and valves wherever possible |
Uniform Corrosion | Limit or prevent this by an appropriate choice of alloy |
Pitting Corrosion | High resistance to pitting will be a crucial consideration point for any alloy |
Stress Corrosion Cracking | Avoid surface machining stresses. Stress cracking resistance needed. |
Aqueous Corrosion | Metals with fantastic seawater resistance Eg. Inconel 625 |
Please apply for our FREE A5 Guide in the Selection Of Special Metals For Tube Fittings and Valves
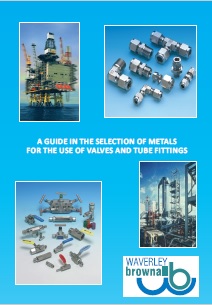
Free guide posted to your business address
Includes:
– Corrosion Resistance Charts
-Availability and Costing
-Delivery and Manufacture
-Material properties
Monel 400, Incoloy, Inconel, Hastelloy and more