
The corrosion of metals is the destructive attack of an alloy and its material properties by an external environment.
With roughly 71% of the Earth’s surface being water, it’s not surprising that aqueous corrosion is such a big concern.
If left to corrode, metal (as part of large structures such as those in the offshore industry) can cause devastating damage.
4 Types Of Aqueous Corrosion
Galvanic Corrosion
This is the most basic form of aqueous corrosion. It occurs when two metals have physical or electrical contact with each other and are immersed in a (liquid) common electrolyte. A car battery is a common example of galvanic corrosion at work, the natural process of corrosion is used to supply electrical energy.
Filiform Corrosion
Filiform is actually a type of Galvanic corrosion that can often be seen on painted alloy engine components working in harsh industrial environments. The thread-like corrosion can appear on coated metals such as steel, iron and even zinc.

Continue scrolling for prevention tips.
Pitting Corrosion
Pitting is one of the most commonly known types of corrosion that can happen to a range of alloys. It is a gradual breakdown of the metals surface. In this type of corrosion, it tends to penetrate the metal rather than spread and this is particularly notable on horizontal surfaces where gravity affects the intensity of the pitting.
Crevice Corrosion
As the name suggests, this type of corrosion is seen commonly in areas where metals are overlapping or areas of cracking. This occurs when one part of a metal is exposed to a different oxygen concentration than other parts. It is not a corrosion type that is exclusive to stainless steels – it can also effect other alloys such as aluminium and copper.
How can Aqueous Corrosion be prevented?
1. One way in which many industries are working against corrosion is to cover their alloys in a resistance coating.
“Rising demand for high performance anti-corrosion coatings in oil & gas, marine, power generation, construction, and other industries is estimated to positively impact the market growth by 2023.”
Source: High performance anti-corrosion coatings, High demand from emerging economies boosts market, industry outlook 2016 to 2023 by Transparency Market Research and Your Oil and Gas News
2. The use of special metals on instrumentation, valves, fittings and pipeline can help prevent the effects of corrosion. High performance alloys that counter aqueous corrosion are especially useful for industries such as Offshore, to be used on rigs and piping applications.
Waverley Brownall are proud to supply numerous companies where seawater is one of the biggest issues facing the performance of an alloy. Our engineers understand the severity of corrosion issues and work towards providing the best solutions to prevent costly – and potentially, life-threatening problems.
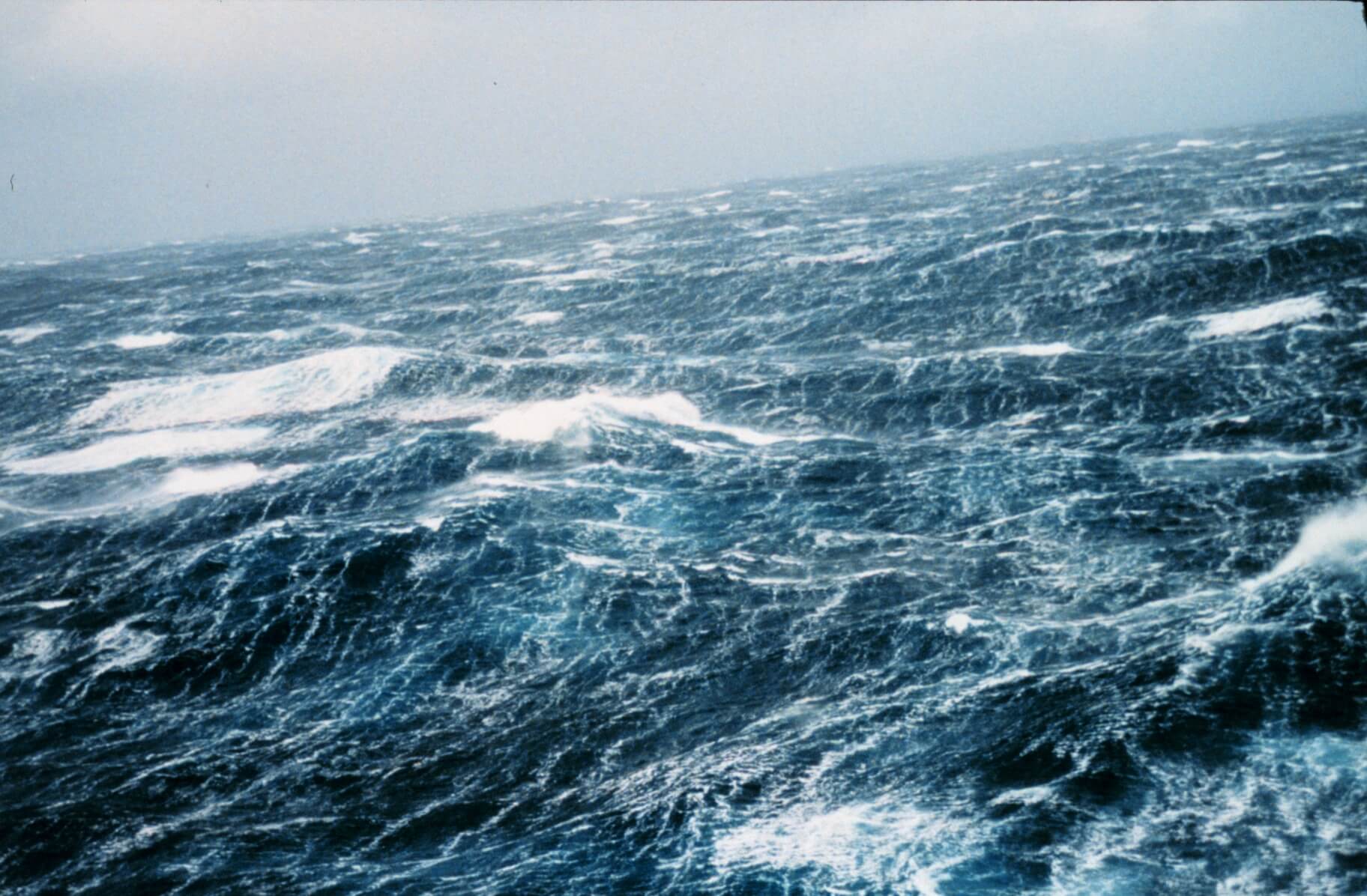
Corrosion
Learn more about the selection of special metals for corrosive environments.
Covering atmospheric and acidic demands.