
Corrosion resistant alloys are used extensively within the marine industry.
Applications where seawater is present requires tough alloys that are able to withstand corrosive surroundings.
Corrosion Resistant Alloys
Seawater can have devastating effects on metals such as iron where the surface of the metal will be attacked relentlessly. However, certain high-performance metals will give longevity and durability if they hold a number of certain properties.
Inconel and Monel are two special metals that perform highly within the marine industry. This section will cover the advantages of using these materials within fittings and valves in an aqueous environment.
Monel 400 Alloy
The nickel-based alloy MONEL 400 offers high strength and of course, corrosion resistance. It is an excellent choice for applications where seawater will be attacking the metal fitting, tube or valve.
Inconel 625
INCONEL 625 offers high resistance against pitting and crevice corrosion. Its high tensile strength makes it the perfect alloy for items such as propeller blades. Inconel 625 ranks within Class I of alloys that are most resistant to the marine environment.

625 has good corrosion fatigue strength when seawater is present. Poorer performances will be seen from alloys such as k-500 or x-750, however, this is in regard to evidence of pitting within stagnant seawater.*
* Versatile Corrosion Resistance of INCONEL alloy 625 in Various Aqueous and Chemical Processing Environments, Presented by Inco Alloys International Inc.
Titanium
Titanium is another metal that holds corrosion resistance properties. It can resist the effects of corrosion within fresh water or steam in temperatures up to 316°C. The temperature of resistance for seawater sits at 260°C. Deposits from marine environments may form, but pitting and crevice corrosion will be completely absent from the alloy itself.
Titanium is considered to be one of the best metals for seawater elements, it is perfect for splash zones and ASTM Grade 2 is essentially immune to seawater stress corrosion cracking. *Offered as a material for fittings and valves by Waverley Brownall.
This hardy material is known for its expense, but alloys with such strong resistances are an investment for the long-term health of structures such as offshore platforms as fatigue will not be an issue with the presence of seawater.
We offer material choices such as Hastelloy C276 and Incoloy 825.
In flowing and stagnant seawater conditions, Hastelloy C276 and Inconel 625 materials give excellent corrosion resistance. Inconel 825 can be susceptible to bio-fueling.
Corrosion Prevention

Corrosion resistant alloys do not need the consistent maintenance or treatments that other metals may require. Titanium or other metals that work well within the marine industry are investments that will secure health, safety and efficiency of the application in question for years to come.
It is cost-effective for companies in the long term, considering maintenance costs and installation replacements are virtually non-existent within a much longer time frame.
Some fittings manufacturers will charge for a full replacement of tube and fitting after 5 years – with alloys such as Titanium, this will be prolonged substantially.
Titanium alloys are known to be difficult-to-machine materials, which causes an even higher price-tag for fittings and valves. However – Waverley Brownall have been machining titanium alloys for over 40 years with specialist knowledge.
We are happy to take orders for titanium fittings for companies who are willing to invest in this incredible solution.
Types Of Corrosion Within A Marine Environment
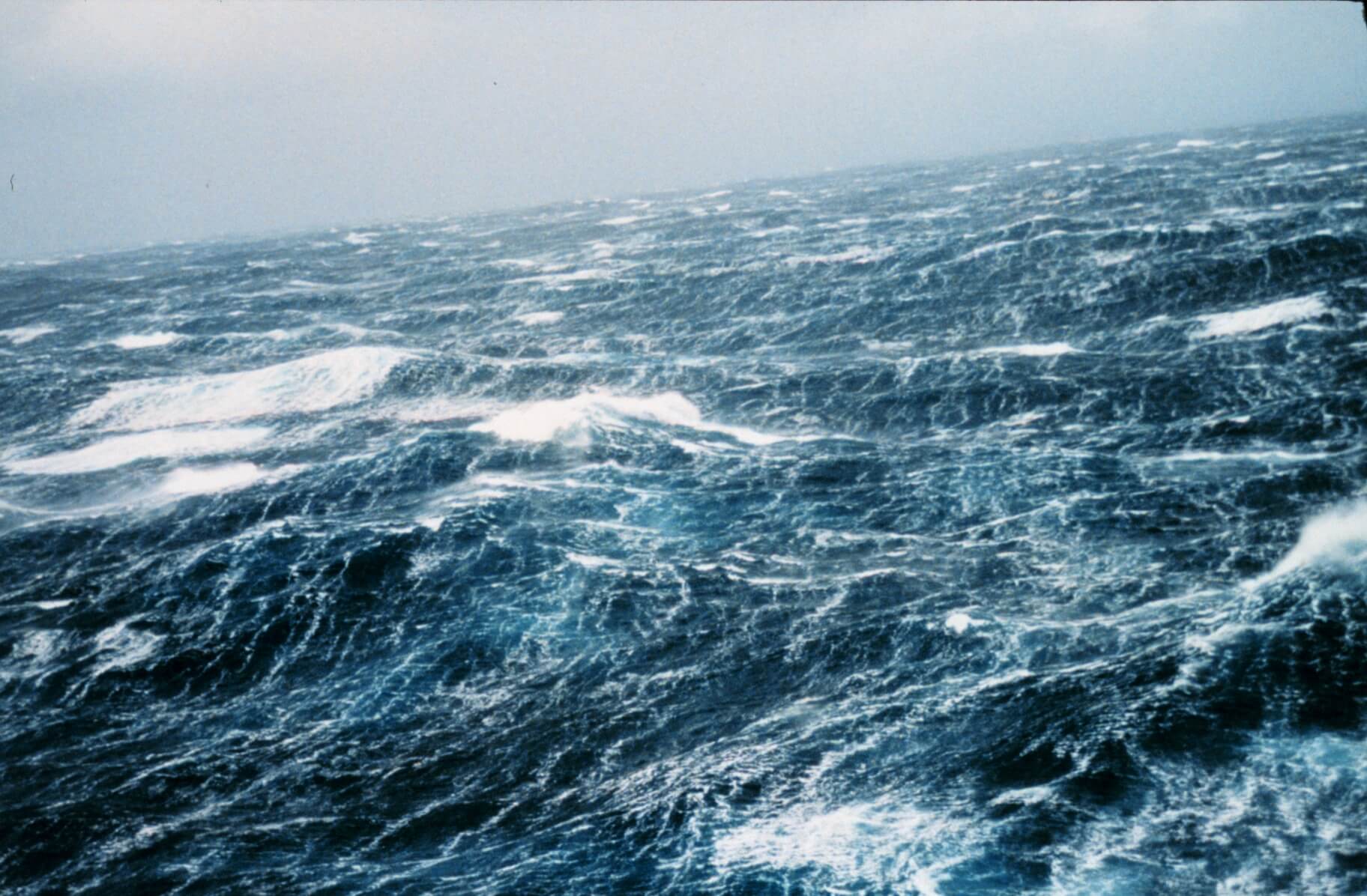
- Galvanic corrosion
- Intergranular corrosion
- Stress corrosion cracking
- Crevice corrosionm
- Erosion corrosion
- Marine growth
Seawater environments can be divided into three main zones.
Zone 1) The first zone covers alloys that are fully immersed or continuously submerged.
Zone 2) Partially immersed such as tidal environments and splash zones .
Zone 3) Zone 3 covers corrosion that is predominantly due to the surrounding environment. As an example, this covers atmospheric and subsoil factors.
Zone 1, Submerged – The main elements that will impact the level of corrosion are temperature, oxygen levels, bio-fueling and pollution. For example, with our standard stainless steel products, pitting and crevice corrosion are the most common concerns for 316 in Zone 1.
For Zone 2 (partially submerged) for areas such as the splash zone, stainless steel has a much higher pitting corrosion rate due to oxygen exposure.
Alloy Selection For The Marine Industry
Do you require more information on the selection of special metals for a range of industries?
We are offering our readers a FREE GUIDE to assist you!

A Guide In The Selection Of Special Metals
FREE GUIDE
Posted for free directly to your address
Presented by Waverley Brownall Limited
Your A5 sized handbook will be posted to the address that
you fill out and submit in the form.
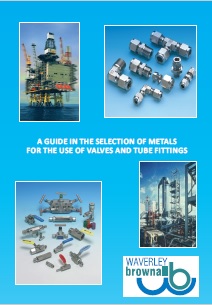
Your guide will include:
- Corrosion by acids
- Corrosion by alkali and salts
- Aqueous corrosion resistance chart
- Material composition chart
- The benefits and properties of each metal we offer