
The issue of corrosion within industries such as oil and gas, chemical processing and marine engineering is extremely important.
To avoid extreme health and safety issues and economic loss, businesses within these industries must be one step ahead of the corrosive media in the working environment.
Solutions for corrosion resistance are available in forms of coatings, but for long-term investment in corrosion resistance, material selection is the number one prevention tool.
Corrosion Prevention Material Selection: The Importance To All Industries
Selecting the correct material to withstand destructive acids, oxygen and waters is the key to avoiding disasters.
This is not only a consideration for economic factors, but industries must prevent disasters on a huge scale that include loss of life, such as the Guadalajara Sewer Explosion. This explosion resulted in the death of 215 people, with 1,500 injured and damage to 1,600 buildings within the surrounding area. You can read more about the explosion in this post on Some Of The Worst Cases Of Corrosion.
Prevention Of Corrosion
Topics covered in this Slideshare include corrosion prevention methods and the considerations regarding material selection for corrosion prevention efficiency.
Slideshare presentation original works by Professor TKG Namboodhiri,
Consultant in Metallurgy and Corrosion
Corrosion Prevention Material Selection
Materials that are used for their corrosion resistance are often called high-performance alloys, special metals, exotic alloys or exotic metals.
Special Metals (Corrosion-Resistant Metals)
Some metals hold the properties to withstand corrosive environments, alongside issues of pitting, stress-corrosion cracking and more. These metals are more expensive than a standard stainless steel, but they can provide strength within environments with acids, alkaline, salts and seawater.
Not every company can have a qualified metallurgist at hand, luckily, there is plenty of information available from the original creators of certain special metals available online. Such as, Haynes International’s information on the alloy Hastelloy-C276.
Waverley Brownall also offer a free book to help guide you in the selection of our range of special metals for extreme applications. This includes information on the main considerations such as availability, metal composition and corrosion resistance charts for a clear view of a metals resistance in comparison to each other.
Considerations For Metal Selection
- Cost of investment (Short term VS. Long term)
- Properties of material needed
- Application of material
- Product of material (Eg. Fittings, Valve)
- Design
- Material VS. Material comparisons to find the best solution
- Technical advice
- Industry requirements and regulations
Materials With High Corrosion Resistance
Metals that hold high-corrosion resistant properties include: Incoloy 825, Inconel 625, Hastelloy C-276, Titanium, Super Duplex, Duplex, 6MO. You can find out more about these on our special metals page.
Learn More With A Free Guide
This guide covers everything you need to know for selecting the right corrosion resistant material for our entire range of valves and fittings.
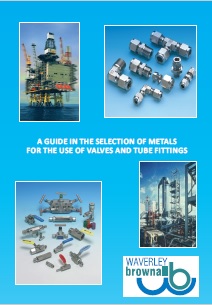
A Guide In The Selection Of Special Metals
*Posted FREE to your address
- Corrosion charts
- Applications
- Strengths
- Alloy properties and Composition
Corrosion Resistant Alloys In Oil And Gas Production
As an approved supplier to Conoco Phillips, BP and Shell, we fully understand the need for correct corrosion prevention material selection within Oil and Gas. Metals within an environment such as this are expected to thrive with external attacks from severe application and heavy usage over a long period of time. This is why we have specialised in manufacturing fittings and valves in special metals to not only cope in these conditions, but to provide the biggest value to engineers around the world.
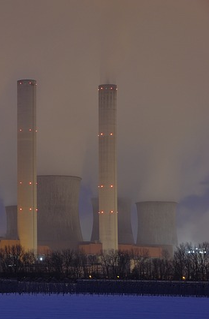
Other Industries
- Chemical
- Processing
- Purification/Water
- Agriculture
- Pump and Valve
- Petroleum
- Renewable Energy
- Nuclear